The natural choice
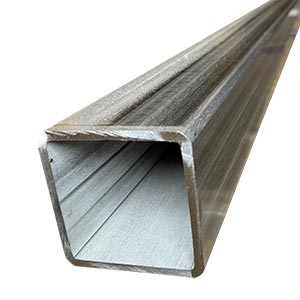
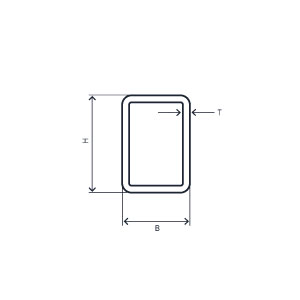
Produktinformasjon
Austenittiske stål med betegnelsene 1.4301 og 1.4307 er de vanligste rustfrie typene og inneholder ca. 18 % krom og 9 % nikkel. Forskjellen mellom de to karakterene er at i 1.4301 er maksimalt tillatt karboninnhold høyere enn for 1.4307 som kan bety at 1.4301 har marginalt høyere styrke. I kritiske situasjoner er midlertidig 1.4307 det foretrukne alternativet siden korrosjonsmotstanden i nærheten av sveisen kan bli svekket for 1.4301.
I forholdet til grunnstålet er hulprofiler av 1.43017/ 1.4307 standardisert i EN10088-2 og 10088-4. mens toleranser og profilegenskaper er som fastsatt i EN10219-2. Tibnors program dekker seksjoner med bredde 15 – 400 mm, høyde 10 – 300 mm og tykkelse 1,2 – 12,5 mm. Utgangsmaterialet for fremstilling av hulprofiler er kald- eller varmebehandlet bånd (glødet, syltet, overflate 1D eller 2B) som er slisset, formet til et kvadratisk eller rektangulært format og sveiset i lengderetningen. Sveisemetodene varierer, eksempler er plasma/TIG, laser- eller stumpsveising. Som en siste operasjon forbedres utseendet til det sveisede området ved sliping.
Gradene 1.4301 og 1.4307 viser god motstand mot korrosjon i nøytralt vann, både innendørs og utendørs. Stålet er også ganske immun mot atmosfærisk korrosjon. De er midlertidig mindre egnet hvis miljøet er surt eller inneholder klorider. I slike tilfeller vil høyere legerte karakterer være nødvendig.
Både 1.4301 og 1.4307 er preget av utmerket formbarhet og sveisbarhet, slik at sveising, bøying eller annen kaldforming av hule seksjoner sjelden er et problem ved behov. Omfattende testing garanterer sveisekvalitet slik at risikoen for sprekker i nærheten av sveisen i forbindelse med bøying eller kaldforming er minimal.
Hulprofiler i klasse 1.4301/ 1.4307 tilbys med to overflateutførelser: ubehandlet med det sveisede området slipt for å fjerne oksid, men sveisen fortsatt helt synlig, eller med hele flatene slipt (korn 220, Ra 1.0 -1,4 µm). Toleranser er spesifisert i detalj i EN 10219-2, men er maksimalt ±10% eller ±0.5 mm for tykkelse. Rettheten er god, med tillatt buehøyde på maksimalt 0, 00015 ganger lengde.