The natural choice
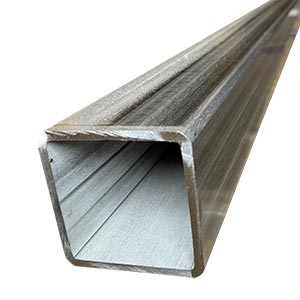

Produktinformasjon
Det austenittiske stålet med betegnelsen 1.4404 inneholder ca. 2 % molybden i tillegg til krom og nikkel. Forskjellen mot 1.4301 og 1.4307 bortsett fra tilstedeværelsen av molybden er at nikkelinnholdet er større. Denne typen rustfritt stål omtales ofte som syrebestandig, noe som til en viss grad er en feilbetegnelse siden materialet motstår angrep kun av svake syrer. 1.4404 har lavt karboninnhold som gjør at den kan sveises uten å risikere svekkelse av korrosjonsmotstanden i nærheten av sveisen. Når det gjelder styrke, tilsvarer 1.4404 mer eller mindre de lavere legerte karakterene 1.4301/ 1.4307.
I forhold til grunnstålet er hulprofiler av 1.4404 standardisert i EN 10088-2 og 10088-4, mens toleranser og profilegenskaper er som fastsatt i EN10219-2. Tibnors program dekker seksjoner med bredde 25-100 mm, høyde 25-100mm og tykkelse 2-5 mm. Utgangsmaterialet for fremstilling av hulprofiler er kald- eller varmbehandlet bånd (glødet og syltet, overflate 1D eller 2B) som er slisset, formet til et kvadratisk eller rektangulært format og sveiset i lengderetningen. Sveisemetodene varierer, eksempler er plasma/ TIG- laser eller stumpsveising. Som en siste operasjon forbedres utseendet til det sveisede området ved sliping.
Tilstedeværelsen av molybden sammen med krom gjør 1.4404 motstandsdyktig mot korrosjon i svake syrer og vann som inneholder klorider så lenge kloridkonsentrasjonen ikke er for høy; et eksempel på et miljø hvor stålet fungerer godt er saltholdig kystatmosfære.
1.4404 kjennetegnes ved utmerket formbarhet og sveisbarhet, slik at sveising, bøying eller annen kaldforming av hulprofiler sjelden er et problem ved behov. Omfattende testing garanterer sveisekvalitet slik at risikoen for sprekker i nærheten av sveisen i forbindelse med bøying eller kaldforming er minimal.
Hule seksjoner i klasse 1.4404 tilbys med to overflateutførelser: ubehandlet med det sveisede området slipt for å fjerne oksid, men sveisen fortsatt helt synlig, eller med hele flaten slipt (korn 220, Ra 1,0 -1,4 µm). Toleranser er spesifisert i detalj i EN 10219-2, men er maksimalt ± 0,6 -1,0 % eller ±0.5 mm for bredde (avhengig av dimensjon) og ± 10 % eller ±0.5 mm for tykkelse. Rettheten er god, med tillatt buehøyde på maksimalt 0, 00015 ganger lengde.